A new hip, a new era: Meticuly, a Thai startup, is rewriting the rules of surgery with on-site 3D printing
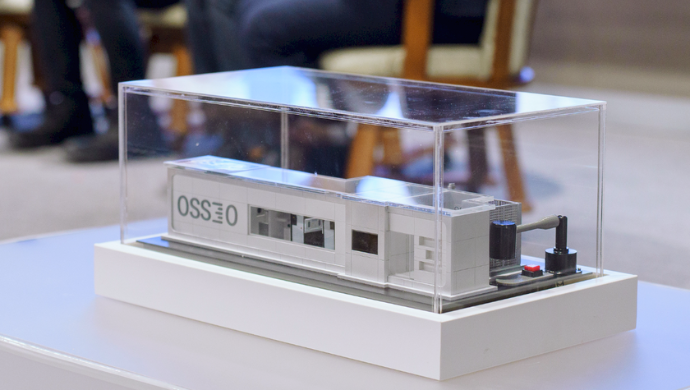
Model of the “Factory-in-a-Box”
It was just after dawn when Mr. Boonrod, a soft-spoken man in his sixties, was wheeled into the operating theatre at Siriraj Hospital. The room was a blur of gloved hands, the hum of machines, and the focused calm of the surgical team led by Professor Dr. Keerati Chareancholvanich. But a quiet revolution was already underway — not just in Boonrod’s failing hip, but in the very way medicine could be practised.
Less than 30 meters away, nestled discreetly inside a container-sized facility tucked within hospital walls, a titanium hip socket had been born. It wasn’t shipped from abroad. It wasn’t manufactured months in advance. It had been designed, printed, and refined right there — in what Siriraj Hospital calls its “Factory-in-a-Box.”
This was not just surgery. It was a signal flare for the future of personalised medicine.
Precision, packaged
On April 2, 2025, Siriraj Hospital — Thailand’s oldest and most prestigious medical institution — announced a world-first: the successful use of a 3D-printed hip implant manufactured on-site using a self-contained modular production unit developed by OSS3O, a joint venture between the Thai startup Meticuly and entrepreneur Tee Thirakomen of MK Group.
The achievement was more than clinical. It was philosophical — a reimagining of healthcare delivery in a system long bound by the constraints of time, distance, and generalisation.
“This is a paradigm shift,” said Asst. Prof. Dr. Chedtha Puncreobutr, Meticuly’s CTO and the OSS3O project lead. “We’ve essentially miniaturised a factory and placed it where it matters most — next to the patient.”
For years, orthopedic surgeries like Boonrod’s — complex revisions of severely damaged hip sockets — have been bottlenecked by the limitations of standard implants. These off-the-shelf devices often struggle to match the anatomical and pathological quirks of patients with degenerative or post-traumatic bone loss. Surgeons are forced to improvise. Patients wait. Outcomes vary.
Not this time.
With OSS3O’s system, engineers worked in lockstep with surgeons, translating CT scans into bespoke implant designs, then printing them on-site using titanium — strong, biocompatible, and tailor-made. All within days, not weeks. And crucially, without the supply chain delays that plague even the most modern hospitals.
Also Read: Decoding digital preferences: A glimpse into the future of health tech ecosystem in SEA
From concept to incision
The so-called “Factory-in-a-Box” might sound like a tech buzzword, but at Siriraj, it’s a working reality. The system comprises a tightly integrated network of advanced manufacturing equipment, robotics, and AI-driven software that transforms clinical imaging data into finished, sterilised implants — all in one container-sized unit.
For Dr. Chareancholvanich, the implications are vast.
“In Mr. Boonrod’s case, the socket was extensively degraded. No commercial implant would have fit securely,” he explained. “But with a custom implant made specifically for him, we achieved a stable reconstruction with less surgical time and trauma.”
The difference is not just in medical jargon, but in human experience: less time under anesthesia, reduced blood loss, and a faster recovery — the metrics that matter most when your mobility, dignity, and independence hang in the balance.
Healthcare, reimagined locally
The success of Boonrod’s surgery is a proof of concept not just for Thailand but for any nation grappling with aging populations and overburdened health systems. By bringing the means of production to the point of care, hospitals can bypass the traditional logistical chains — often expensive, bureaucratic, and international.
“Imagine a world where every hospital has its own digital manufacturing hub,” said Dr. Apichat Asavamongkolkul, Dean of the Faculty of Medicine at Siriraj. “From facial trauma to orthopedic reconstructions to tumor-related resections — everything personalised, everything fast.”
The OSS3O initiative is backed by the Program Management Unit for Competitiveness (PMUC), a Thai government agency aiming to elevate the country’s technological capabilities in healthcare. But its success is also a function of synergy — between startups like Meticuly, academic institutions like Mahidol University, and private industry players who see healthcare innovation not as charity, but as a growth strategy with global reach.
Also Read: Striking the right balance: Financial health, talent retention, and business growth
Meticuly, which already holds regulatory clearances from both Thai and U.S. FDA authorities, believes this is just the beginning. The company has helped over 2,000 patients so far and is scaling to treat 10,000 annually. With 36 patents across 10 countries and ambitions to embed “Factory-in-a-Box” units in hospitals worldwide, its vision feels more inevitable than aspirational.
Beyond the operating room
While the titanium hip socket may grab headlines, the broader application of this technology is quietly even more transformative. The on-site system is already producing custom facial plates for orbital injuries, mandibles for cancer survivors, and joint replacements for children with congenital deformities. It is, in essence, a symphony of science and empathy — a bridge between engineering and healing.
“This isn’t about machines replacing doctors,” Dr. Puncreobutr said. “It’s about enabling doctors to do what they do best — but with better tools, better precision, and better timing.”
And for Mr. Boonrod, it means walking again. Not with a standard implant designed for a theoretical average person, but with one made uniquely for him.
As he stood with assistance days after the procedure, flexing the leg that once betrayed him, there was something poetic in the fusion of metal and medicine. A quiet triumph. A glimpse of the future — forged not in a distant factory, but in a container behind the surgery ward.
—
This article was originally published on The Startup Booster Substack.
Editor’s note: e27 aims to foster thought leadership by publishing views from the community. Share your opinion by submitting an article, video, podcast, or infographic.
Join us on Instagram, Facebook, X, and LinkedIn to stay connected.
We’re building the most useful WA community for founders and enablers. Join here and be part of it.
Image courtesy: Meticuly
The post A new hip, a new era: Meticuly, a Thai startup, is rewriting the rules of surgery with on-site 3D printing appeared first on e27.